Industry-Sponsored Student Capstone Projects
2024/2025
In the 2024/25 academic year the industry capstone program was supported by 65 sponsors, more than half of which were returning, and 96 real-world projects. Over five hundred fifty students from across the College of Engineering participated. Scroll down to learn more about each project.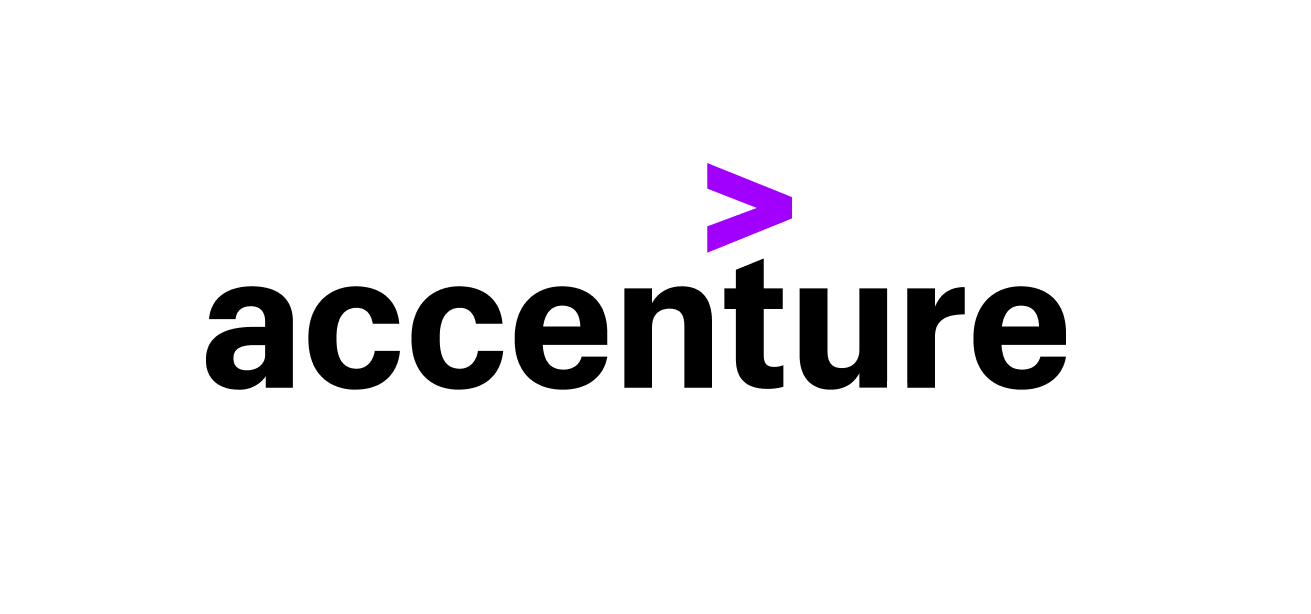
Accenture + Grokit
Intelligent Human + Robot Work Cell Simulation and Orchestration
This student team will work to build an interactive demo (simulation, visualization/dashboard, physical robots) showcasing workflows where humans and robots work dynamically together with a distributed intelligence engine (Grokit's Paranet) optimizing resources/skills and reassigning robots in rea-time without recoding. The Problem Statement this student team will work to address is to orchestrate humans and robots in a dynamic workcell to complete tasks based on their skills and abilities matching, and seamlessly reassign resources between workflows without additional technical steps. The objectives this student team will work to achieve include, in real-time, showcase an intelligence engine instructing robots and humans to seamlessly change their actions based on the user selected workflow in real time, while in close collaboration with a human operator within the process - simulated and digital/physical.
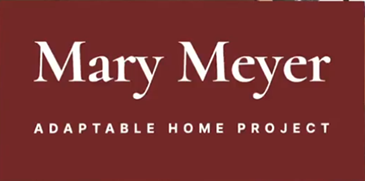
Adaptable House
Overhead Mobility Full-Support System for Adaptable House
The Adaptable House Project seeks to answer problems of well-being and movement in the home of aging and physically challenged people. This student team will work to design and build a model living house for living life at maximum freedom, that would evolve with the special needs and unique challenges of each person. This student team will work to design a mobility system that would avoid the limitations of traditional wheelchair and walkers by using an overhead gantry and track system to assist the user with three different levels of support. In particular, this student team will work to design, build, and test a better "hanging chair" that is a key component of the integrated mobility system for the Adaptable House Project. The hanging seat is the interface between the user and the mobility system. The desired outcomes this student team will work to achieve are an aesthetically pleasing, inspiring, playful seating system that supports the multiple use modes and is simple/easy to use.
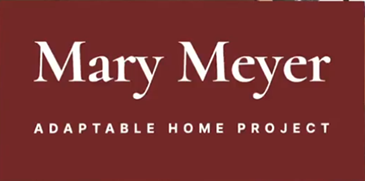
Adaptable House
Overhead Mobility Handhold System for Adaptable House
The Adaptable House Project seeks to answer problems of well-being and movement in the home of aging and physically challenged people. This student team will work to design and build a model living house for living life at maximum freedom. The living house would evolve with the special needs and unique challenges of each person. This student team will work to design a mobility system that would provide a user with multiple ways to move themselves through the house. The desired outcomes this student team will work to achieve are an aesthetically pleasing, inspiring, playful hanging system that supports the multiple use modes and is simple/easy to use. This student team will work to create a preliminary design and scaled prototyping of a system of hanging bars and track that enables a user to stretch, move forward, and hang as they move throughout the house.

AeroTEC
Low Cost Wind Tunnel Testing for Rapid S&C Development Testing
This student team will work to build up data sets to support low cost wind tunnel and analysis methodologies that allow for rapid development of stability and control parameters for new configurations or modifications to existing aircraft. This student team will work to build off of past testing and develop a new data set based on a trade study for low speed aircraft (C182 or similar) and trade studies for best low cost manufacturing techniques. Design parameters and performance this student team will work to incorporate include: - Cost, schedule, quality trades for model cost, materials, and construction techniques. - Basic stability and control parameters for light aircraft. - % error relative to published data sets considered accurate. The outcomes this student team will work to achieve are: - a data set analysis for existing wind tunnel data - Business Jet and Supersonic configurations (Already tested at KWT, public non-proprietary data) for cost and accuracy - a generation of additional data set for low speed configuration (C182 or similar) - the development of a wind tunnel model for low speed configuration - trade studies for lowest cost design and manufacturing methods

AeroTEC
UAV Health Monitoring and Flight Test Development Phase III
In the past, the AeroTEC capstone projects have focused on supersonic and highly efficient structural aircraft designs. This student team will work to capitalize on past work developed as part of the Aircraft Design Capstone programs, specifically in Phase I and Phase II, developing flying UAV for use as flight test beds for advanced R&D. AeroTEC will use the Phase II aircraft for additional research and development in the areas of modeling, simulation, data acquisition, telemetry systems and machine learning. The '24/25 AeroTEC student team will work to develop a program and capabilities that will allow future students to test designs in a controlled environment using industry standard best practices. For phase III this student team will work to further develop the aircraft health monitoring system and machine learning techniques for data analysis as well as learn telemetry and flight test best practices. This student team will work to focus on the phase II aircraft and health monitoring system. The student team will be responsible for prepping the flight test aircraft and conducting a Safety of Flight Review. Students will be responsible for providing research and data to support AeroTEC getting flight permits for FAA flight clearance at AeroTEC's Moses Lake facility for fight testing. The student team will work to further develop simulation models in key areas of S&C, FEM and performance for prediction of key flight characteristics and structural dynamics from Phase II's takeoff point. This student team will also work to provide specification of key instrumentation to allow for comparison of flight test data to simulator data. Additionally, this student team will work to develop a low cost aircraft health monitoring system (with support from AeroTEC) that can be installed on the aircraft and record structural health data. This will flow from Phase II's work. The outcomes this student team will work to achieve are: - Further development of one of the flight test articles that can be used for flight test development programs (Phase II Truss Braced Wing). - Flight of a UAV under remote and autonomous control and BLOS flight. - Execution of a SOF review before flight release, - Further development flight simulator and the structural health monitoring system. - Further development Telemetry system and Beyond Line of Sight testing.
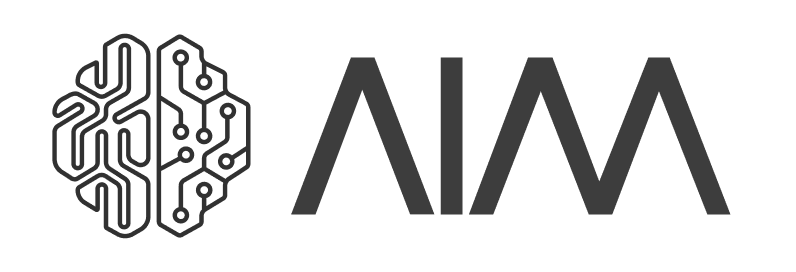
AIM Intelligent Machines
Loader Design and Simulation for Vibration Testing and Bash Guard Optimization
Part of AIM's mission is to automate existing machinery. This student team will work to take the first steps towards automating a loader. The students will work to add on an inclinometer to the bucket so that AI can use the data to operate it. The student team will work to first model the loader in a simulation that will eventually be applied to the real machines. FEA will be used to evaluate the effectiveness of the sensor's mount and a simulation will be used to test the environment of the loader. The student team will work to create a mount on the bucket that will secure the current inclinometer used, handle the typical loads and vibrations at the chosen location, meet a FoS of at least 1.5, and accurately measure the location of the bucket. The student team will work to make a loader in SpaceClaim to load into the existing simulation, appropriate damping and environment needs to be determined. The outcomes this student team will work to achieve are: - an accurately modeled existing CAT loader with working mechanics - a successful simulation of a typical environment of a loader, - designed a bash guard for an inclinometer sensor that withstands the types of forces found - optimized the location and manufacturability of the bash guard, and - run FEA on the bash guard to determine it's life.
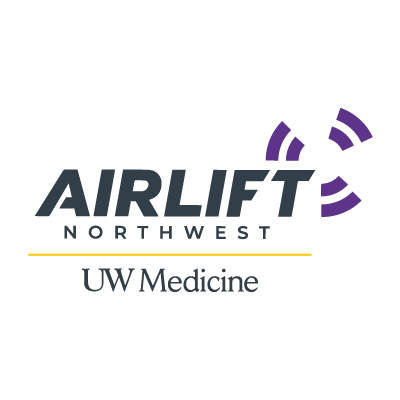
Airlift Northwest/UW Medicine
Blood Management in Air Transport
Airlift Northwest/UW Medicine transports more than 4000 patients annually in the Pacific Northwest. Their treatment protocols include the administration of Blood Products for critically ill and traumatically injured patients. The acquisition, distribution, retrieval and return of blood products requires attention to a variety of factors in timing, temperature control and geographical distribution. To effectively manage and administer this part of the Airlift program requires process planning and execution that maintains the viability of the blood products in a dynamic environment. Improvements to the system of delivery would benefit patients and crews as well as positively impact the financial outcomes. The student team will work to review all the ancillary equipment related to managing blood products (cooler boxes, in aircraft spaces, on-base storage) as well as associated processes (i.e. temperature control) and provide a recommendation for improvement. They outcomes will be a set of feasibility studies and prototype tests to justify their recommendation for new temperature control equipment. There is also an industrial systems engineering student team working on evaluating and improving the overall process for procurement, distribution, utilization, and return of the blood products. The ISE and ME teams will collaborate to share insight to lead to effective, systems-level solutions.
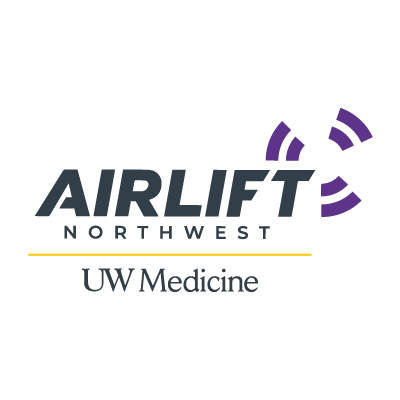
Airlift Northwest/UW Medicine
Blood Managment in Air Transport
Airlift Northwest/UW Medicine transports more than 4000 patients annually in the Pacific Northwest. Their treatment protocols include the administration of Blood Products for critically ill and traumatically injured patients. The acquisition, distribution, retrieval and return of blood products requires attention to a variety of factors in timing, temperature control and geographical distribution. To effectively manage and administer this part of the Airlift program requires process planning and execution that maintains the viability of the blood products in a dynamic environment. Improvements to the system of delivery would benefit patients and crews as well as positively impact the financial outcomes. The student team will work to review procurement (UW Blood Bank --> Airlift), Distribution & Storage (8 bases across Washington and Alaska), and maintaining product viability (expiration dating) and returning of product. The outcomes will be recommendations for improvement or process redesign in any aspect of the Blood delivery process including human factors. There is also a mechanical engineering student team working specifically on the ancillary equipment related to managing blood products (cooler boxes, in aircraft spaces, on-base storage) as well as associated monitoring (i.e. temperature control). The ISE and ME teams will collaborate to share insight to lead to effective, systems-level solutions.

Amazon
Multi-Robot 3D Scanner
This student team will work to design and develop a multi-robot 3D scanner which can handle and scan a variety of objects of different shapes and sizes and produce even and detailed scans of the entire part with little to no obfuscation or unscanned areas. Students will use an off-the-shelf or in-house developed 3D scanner which can produce detailed, full-color 3D scans of the parts, and the resulting 3D models should be noise-free and watertight. The solution the students work to develop should implement multiple robots which work together to scan all areas of the part without obfuscation, which may require adjusting grip one or multiple times. The solution the students work to develop should also be robust and adaptable to a wide variety of parts and should be accurate in terms of dimensions and colors. This project has some hard constraints, but is otherwise relatively open-ended. The solution the students work to develop should be flexible and adaptable, and should be able to handle and scan a variety of parts ranging in shape and size. The solution should involve multiple robots, all interacting together. At a minimum, there should be two robots interacting together, but students are allowed and encouraged to use more than two robots. How the student group chooses to implement this requirement is up to them. Students could approach this with one robot holding the scanner and the other manipulating the part, or use a stationary scanner and two arms that manipulate the part together. Students can either use an off-the-shelf scanner or develop their own, but it should utilize two or more of the following scanning technologies, including but no limited to: photogrammetry, depth cameras, LiDAR, laser, and/or another advanced scanning technology that can capture geometry and color. Finally, students should implement detection of obfuscation by robot end effector and implement a repositioning algorithm where the robot adjusts its grip on the part or hands it to another robot to allow all areas of the part to be scanned. The scanner the students work to develop should produce a high-resolution, full-color 3D model. There is no time limit, but shorter scan times (or less number of moves) are preferred (while maintaining accuracy and coverage). Students will be evaluated on accuracy, coverage, repeatability, time to complete/number of moves, and flexibility/adaptability to different objects and shapes. Performance metrics will be discussed and established with the student group and will be used for objective evaluation. Recommended metrics are accuracy (±0.5mm) and coverage (95%), but different metrics and/or values can be used. The overall scope and goals/deliverables of this project shall be discussed with the student group and adjusted if necessary. The main deliverables this student team will work to achieve are: - Multi-robot interaction to handle and scan a variety of parts with different shapes and sizes. At a minimum, students should use two robots, but they are allowed and encouraged to use more. This may require implementation of collision avoidance in the path planning. - Use of an off-the-shelf or homebuilt 3D scanner that utilizes photogrammetry, depth cameras, LiDAR, laser, and/or another advanced scanning technology that can capture geometry and color. - Detection of obfuscation by robot end effector and repositioning (adjusting grip) to allow all areas of the part to be scanned. - Post-processing algorithm (off-the-shelf or custom-developed) that removes background and noise, producing a high-res, watertight 3D model with full-color textures. - Design of a user interface which easily allows users to scan any object and retrieve the data. The stretch goals this student team will work to achieve are: - Even coverage/resolution across the entire model (all areas have the same LoD present). - Use of generative AI to generate/recover details (color, geometry) in areas which may be obfuscated or unscannable. - In the case of non-rigid objects, compensate for deflection or deformations in the shape of the object caused by the robot gripping. - Error detection and recovery: in the event of a crash or movement error, recognize the fault and recover.

Amazon
State Space Model Optimization for Edge AI
State Space Models like Mamba 2 attention compute scales linearly instead of quadratic, which is a benefit. Another benefit is that that KV cache is not scaling linearly but remains constant. Amazon Devices and Services recognizes this benefit as required RAM and compute reduces for such models. However, in addition to the benefits, there is scientific risk that when these models are optimized or quantized they don't maintain accuracy. Thus, this student team will work to invent scientific techniques to quantize and optimize SSM and create multiple optimal models on pareto optimal curve with accuracy and performance. The second part of the project this student team will work to achieve is to run these models accuracy once optimized on edge hardware like Orange Pi or Raspberry Pi using open source frameworks like Ollama, Llama.cpp. Research paper: https://arxiv.org/pdf/2405.21060 Accuracy: Standard benchmarks as defined in LM Harness like Lambada, ARC easy/challenge. Performance Criterion: Accuracy degradation after model optimization and quantization <3% degradation on each task Demonstration: Optimized model running on Edge HW like Orange Pi or Raspberry Pi The outcomes this student team will work to achieve are: Quantized Mamba 2 or equivalent LLM architecture with <3% accuracy degradation on LM Harness Quantized model deployed on Orange Pi using open source frameworks like Ollama, Llama.cpp The bonus deliverables this student team will work to achieve are: Quantized + Sparse (50%) on Mamba 2 or equivalent LLM architecture with <3% accuracy degradation on LM Harness Quantized model deployed on Orange Pi with access of NPU from Rochip on Orange Pi
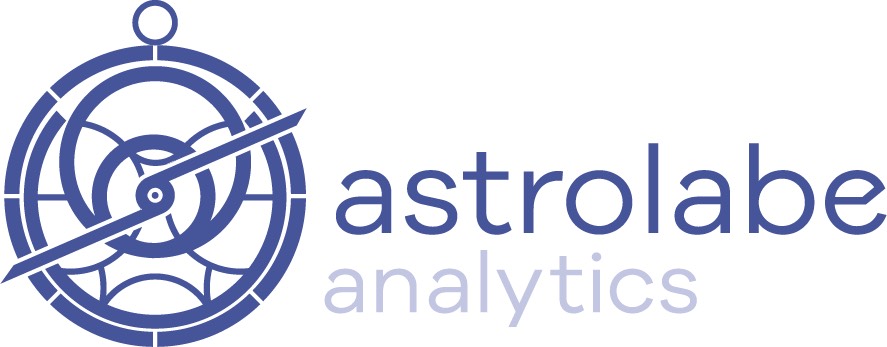
Astrolabe Analytics
Organization and Analysis of Battery Data from Heterogenous Sources
In the rapidly evolving field of energy storage, battery technology plays a crucial role in enabling sustainable solutions. Companies working with batteries often collect vast amounts of data from various sources, such as cell-level and pack-level measurements, cycling tests, and open-circuit voltage experiments. However, this data is typically heterogeneous, originating from different equipment, formats, and naming conventions. The lack of standardization poses significant challenges: • Data Inconsistency: Varying column names, units, and formats make it difficult to aggregate and compare datasets. • Inefficient Data Processing: Data scientists spend considerable time manually cleaning and transforming data before analysis. • Delayed Insights: Slower data processing leads to delays in deriving actionable insights, hindering timely decision-making. These challenges underscore the need for a streamlined process to collect, standardize, and store battery data efficiently. An effective solution would enhance data usability, reduce manual effort, and accelerate the analysis pipeline. This student team will work to develop a web-based portal designed to facilitate the seamless upload and standardization of battery data from diverse sources. The project will encompass both front-end user interface design and back-end data processing, culminating in a functional prototype. The key components of the solution this student team will work to achieve are: 1) User-Friendly Web Portal Potential Flow: Astrolabe Analytics provides access by sending customers a link to access the platform and provide their credentials or basic information such as name, company, and associated project. Once logged in, users can proceed to the data type selection, where they choose the kind of data they wish to upload from predefined categories like discharge data, cycling data, or open circuit voltage data, or specify ‘Other’ for additional types. The portal features an intuitive upload process, supporting drag-and-drop functionality that allows users to efficiently upload multiple files at once. After the upload, the data is tagged with relevant metadata to ensure proper metadata association, linking each dataset to the correct customer and project within the database. 2) Backend Data Management The backend should have the following features: i) Data Standardization Pipeline (can be done in collaboration with Astrolabe Analytics' Lead Data Scientist) a. Automated Transformation: Implement scripts to standardize column names, units, and data formats based on predefined conventions (e.g., using snake_case for column headers like voltage_v, current_a). b. Column Mapping Interface: For datasets with unconventional formats, provide an interface for users to map their columns to standard names during the upload process. c. Error Handling: Detect and flag inconsistencies or missing data for manual review. ii) Data Cataloguing: Standardized datasets are organized and stored, ready for immediate use by data scientists. iii) Cloud Integration - Uploaded files are securely stored on Amazon Web Services (AWS), ensuring scalability and reliability (can be done in collaboration with our Cloud Architect) The outcomes of the design phase that this student team will work to achieve are: • Develop the architecture for both front-end and back-end components. • Create a database schema to store metadata and standardized data. The outcomes of the implementation phase that this student team will work to achieve are: • Build the web portal with user authentication and data upload capabilities. • Develop the data standardization scripts and column mapping interface. • Integrate AWS for file storage and management (interfacing with our Cloud Architect for AWS deployment). The outcomes of the testing and results phase that this student team will work to achieve are: • Validate the system with sample datasets representing various data types. • Demonstrate the reduction in data processing time and improved data consistency. Finally, this student team will work to provide user manuals and technical documentation for future maintenance and scalability.

AvtechTyee
Thermal Test Chamber
This student team will help design, test, and build a modular in height thermal test chamber for use in testing composite rods at elevated temperatures. The chamber should be modular in 2-foot sections with additional various heights, up to 110 inches while being insulated enough to prevent thermal instability inside the chamber. The chamber should have convection heating through a self-contained heating element and controller powerful enough to provide stable temperatures in the range of 225F minimum with 250F as nominal the temperature. The chamber should also have a pivoting front door to help load and unload test specimens as well as several clear viewing windows to allow observation of the specimen during testing. At minimum specimen viewing should be done at the top and bottom modals with one in the center if the full length isn't possible due to insulation purposes. The team will work to create a fully designed, built, and tested solution to meet criteria.
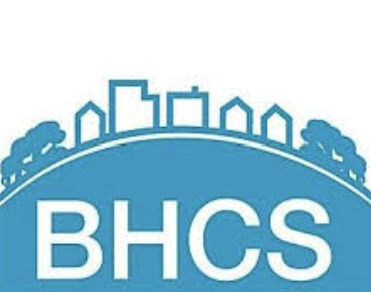
Beacon Hill Community Council
Community Capstones in Clean Energy: Cooling Center Assessment for Beacon Hill
COMMUNITY DESCRIPTION: Beacon Hill is a diverse urban community in Seattle where 70% of the residents identify as black, indigenous, multi-racial, or persons of color; 10% identify as Hispanic/Latinx. A majority of the community speaks a language other than English. Major ground and air transportation corridors border the neighborhood, resulting in disproportionate burden from fossil emissions and noise. Beacon Hill also has low tree canopy cover, making the neighborhood an urban heat island especially vulnerable to increasingly frequent extreme heat events being experienced in the pacific northwest. –––––––––––––––––––––––––––––––––––––––––––––––––––––––––––––––––––––––––––––– PROJECT DESCRIPTION: The Beacon Hill Council has identified several possible locations for community cooling centers that are accessible to their most vulnerable populations during extreme heat events, and days with unsafe air quality. One or more of these sites, based on community input and preliminary technoeconomic analysis, will be evaluated for current energy use patterns and the site’s technical and economic potential for on-site solar energy and energy system upgrades to deliver needed cooling and air-filtering at an affordable electricity cost. The addition of energy storage will be used to assess the added cost to provide resiliency to outages. Project timeline and deliverables will include, at a minimum: • January, 2025: Working with Beacon Hill Council leadership, establish criteria for a community cooling and air quality center, identify several possible sites for preliminary analysis of their technical and economic potential. • February, 2025: Site(s) selection and acquisition of meter data. • March, 2025: Mutually-agreed upon statement of work and baseline data set for analysis. • Spring Quarter, 2025: Carry out statement of work activities tied to understanding annual energy needs and the impact of system upgrades to achieve needed cooling and air quality during extreme weather and smoke events. Energy system analysis may include the technical and economic implications of adding solar energy to reduce the burden of energy costs during extreme weather, adding energy storage to enable ride-through during power outages (which are more likely in extreme weather and forest fire season), and HVAC system upgrades. • May/June, 2025: Final technical report and presentation.

Blue Origin
Design of a Passive Terminal Decelerator
Blue Origin's New Shepard launch vehicle consists of two primary elements: the Propulsion Module (PM) and the Crew Capsule (CC). During a mission, the PM and CC are connected until separation occurs and the two elements descend and land separately. The PM descends until it hits a certain altitude, at which time the engine relights and the PM touches down on the landing pad. The CC descends until it reaches a specific altitude where the Primary Decelerator System (PDS) deploys to slow the vehicle for landing. Just prior to touchdown, the Terminal Decelerator System (TDS) engages to further slow the vehicle for landing. The purpose of the TDS is to provide thrust and energy absorption immediately before and during landing. It consists of two major assemblies: the Active TDS and Passive TDS. The Passive TDS is a consumable item which is replaced after each flight at great cost. Currently, there is not a system to determine whether the Passive TDS components are "damaged" (i.e. there is no way to determine if they have been engaged). Therefore, this student team will work to create a design that meets energy absorption requirements, can withstand the expected operating environment, and is retrofittable. The supplier shall deliver a design package which meets the following requirements: - energy absorbing capability (the student team will refer to a handout of Figure 1, "Pressure vs. Displacement curve" provided by the sponsor) - Fits in the cross-section area (the student team will refer to a handout of Figure 2, "Cross section," provided by the sponsor) - Can operate in environments ranging from desert (scrub brush, hardpan, etc.) to above the Karman line without damage - Can withstand up to 250 F This student team will work to deliver a design package that will include all work showing the proposal meets the requirements discussed in the "design parameters and performance" section such as: - Test Data - Analysis - Cost estimate for design - Evidence the design can be reused while being subjected to environmental conditions expected to be seen during flight.
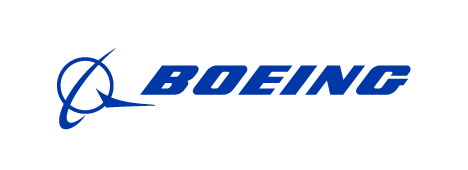
Boeing
Flexible Positive Pressure Consolidation Expandables
Structural composite parts need to undergo high-pressure compaction and heating for curing, which is traditionally done using autoclaves. However, the cost of purchasing and operating an autoclave is significant. In cases where large composite parts that have already been cured in an autoclave require repairs in small areas, returning the large composite part to the autoclave is not cost-effective and causes further production delays, especially in industries like airplane manufacturing. A more effective repair method is needed: a solution that provides local compaction and heating without requiring airtight sealing and another large apparatus, such as an autoclave. This proposal seeks a solution where a localized positive pressure consolidation system that can achieve predetermined pressure of compaction (such as 15-50 psi) for a duration (such as one hour) at a predetermined temperature. This project is a continuation of a previous UW capstone project, which led to a proof-of-concept demonstration unit. This student team will focus on a more flexible system adaptive to curved parts that have the potential to be implemented in the aviation industry. The student team will perform two main technical tasks: 1) Develop a flexible setup that can be adaptive to various geometries. This setup should include features such as a flexible cover and a reaction support plate that can adapt to different shapes to counteract the positive pressure. 2) Monitor and control the pressure generated from the expandable material. The compact pressure should be high enough to create high-quality composite structures or high-quality bonds, but low enough to enable a reasonably reaction support plate to counteract the positive pressure. Additional requirements, such as surface finishes, may be needed depending on the applications. The tool will need to be cleaned after curing. The first two tasks can be based on a co-bond setup between metal and composite doubler. 3) Depending on the success of the first two tasks, a stretch goal is to make composite parts by using the system and compare the parts to two more fabrication methods: autoclave cured method and Double Vacuum Debulk (DVD) cured method. The student team will develop a flexible positive pressure consolidation system by using expandable media. 1. Generate ideas, evaluate them, and create prototypes. Key components include a flexible cover, pressure sensors, fastening elements, and a reaction support plate to withstand positive pressure. 2. Conduct initial validation tests at the component level for selected ideas based on the co-bond setup between metal and composite doubler.
Related News
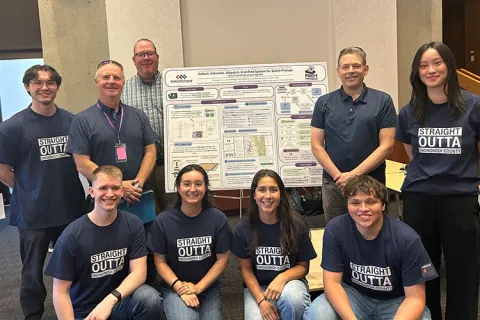
Thu, 07/17/2025
UW engineering students develop smart ballot solution
UW engineering students develop smart technology solution to improve ballot collection for Snohomish County.
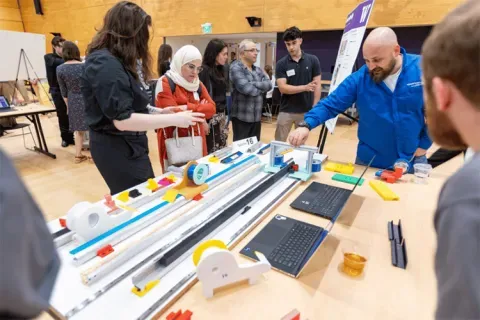
Mon, 07/07/2025 | UW Mechanical Engineering
Capstone creations
Students displayed innovative capstone design projects at the 2025 expo.
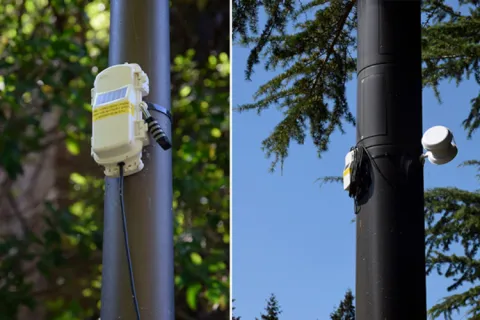
Fri, 09/20/2024 | UW Civil & Environmental Engineering
Smarter irrigation for a greener UW
A new project combines satellite data with ground sensors to conserve water and create a more sustainable campus environment.
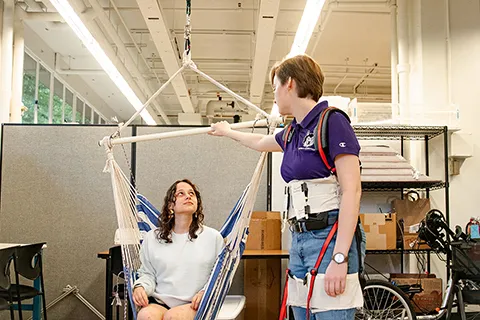
Mon, 09/09/2024 | UW Mechanical Engineering
Testing an in-home mobility system
Through innovative capstone projects, engineering students worked with community members on an adaptable mobility system.