Blue Origin
Design of a Passive Terminal Decelerator
Blue Origin's New Shepard launch vehicle consists of two primary elements: the Propulsion Module (PM) and the Crew Capsule (CC). During a mission, the PM and CC are connected until separation occurs and the two elements descend and land separately. The PM descends until it hits a certain altitude, at which time the engine relights and the PM touches down on the landing pad. The CC descends until it reaches a specific altitude where the Primary Decelerator System (PDS) deploys to slow the vehicle for landing. Just prior to touchdown, the Terminal Decelerator System (TDS) engages to further slow the vehicle for landing. The purpose of the TDS is to provide thrust and energy absorption immediately before and during landing. It consists of two major assemblies: the Active TDS and Passive TDS. The Passive TDS is a consumable item which is replaced after each flight at great cost. Currently, there is not a system to determine whether the Passive TDS components are "damaged" (i.e. there is no way to determine if they have been engaged). Therefore, this student team will work to create a design that meets energy absorption requirements, can withstand the expected operating environment, and is retrofittable. The supplier shall deliver a design package which meets the following requirements: - energy absorbing capability (the student team will refer to a handout of Figure 1, "Pressure vs. Displacement curve" provided by the sponsor) - Fits in the cross-section area (the student team will refer to a handout of Figure 2, "Cross section," provided by the sponsor) - Can operate in environments ranging from desert (scrub brush, hardpan, etc.) to above the Karman line without damage - Can withstand up to 250 F This student team will work to deliver a design package that will include all work showing the proposal meets the requirements discussed in the "design parameters and performance" section such as: - Test Data - Analysis - Cost estimate for design - Evidence the design can be reused while being subjected to environmental conditions expected to be seen during flight.
Faculty Adviser(s)
Junlan Wang, Professor
Related News
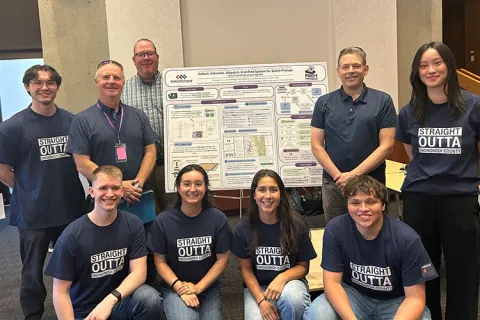
Thu, 07/17/2025
UW engineering students develop smart ballot solution
UW engineering students develop smart technology solution to improve ballot collection for Snohomish County.
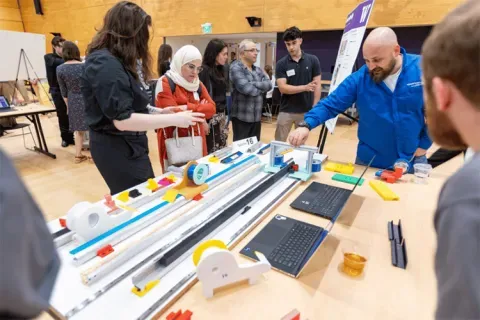
Mon, 07/07/2025 | UW Mechanical Engineering
Capstone creations
Students displayed innovative capstone design projects at the 2025 expo.
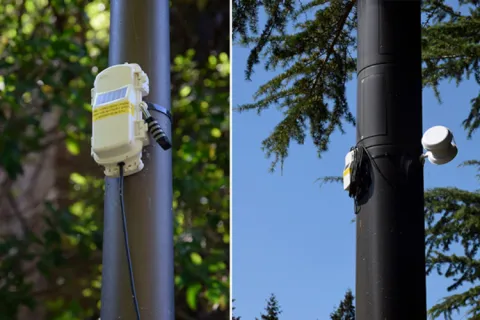
Fri, 09/20/2024 | UW Civil & Environmental Engineering
Smarter irrigation for a greener UW
A new project combines satellite data with ground sensors to conserve water and create a more sustainable campus environment.
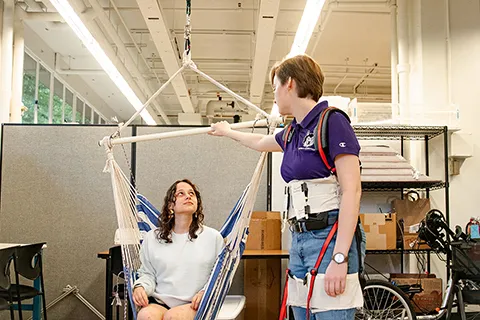
Mon, 09/09/2024 | UW Mechanical Engineering
Testing an in-home mobility system
Through innovative capstone projects, engineering students worked with community members on an adaptable mobility system.