Industry-Sponsored Student Capstone Projects
2024/2025
In the 2024/25 academic year the industry capstone program was supported by 65 sponsors, more than half of which were returning, and 96 real-world projects. Over five hundred fifty students from across the College of Engineering participated. Scroll down to learn more about each project.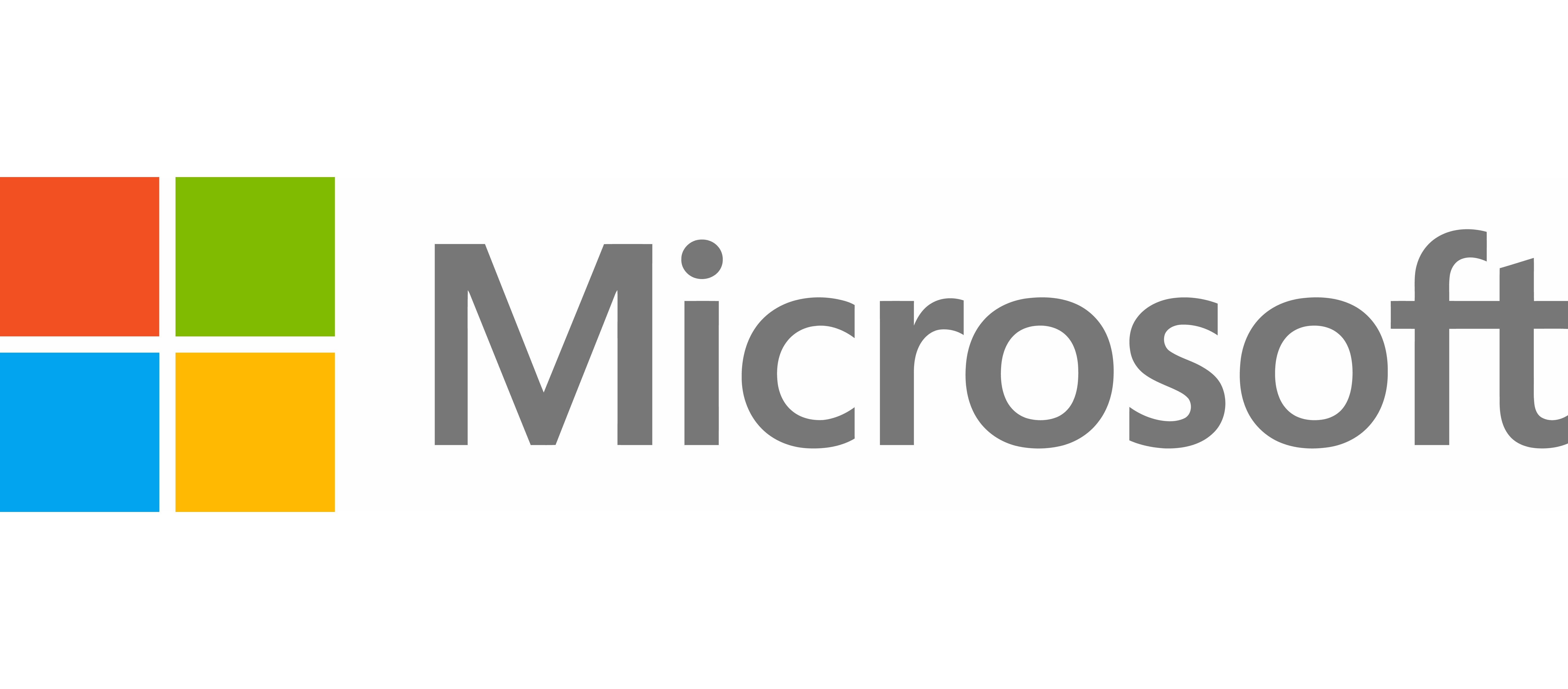
Microsoft
Copilot PC Power Insights
In the first part of the capstone project the student team will work to characterize power consumption across a variety of test cases in Surface Computers. Students will utilize both hardware and software to collect statistical data that is analyzed across system settings, app workloads, and app settings. Because acquiring such data manually would be tedious at best, all aspects that can be automated shall be: data acquisition, test case setup, and data analysis. Machine learning on the output data set will highlight the sources of variability and the effect sizes across conditions. In the second part of the project the student team will build on the first part, leveraging the automation work product to develop a Test App that characterizes the power performance of relevant Apps as determined by the telemetry analytics leadership. Based on previous data, a rating system would be established, and the App under Test (AUT) would receive an energy rating. Requirements: - Detailed planning will be co-developed between Microsoft and the student capstone team. - Computing hardware and any instrumentation will be provided by Microsoft and shall be returned at the end of the project. - All monitoring and development tools shall leverage retail software The student team will work to deliver statistical characterization of Power Consumption of Surface Computers on a variety of scenarios determined by the team. Emphasis will be put in Design of Experiments to help understand power consumption behaviors representing real use cases.
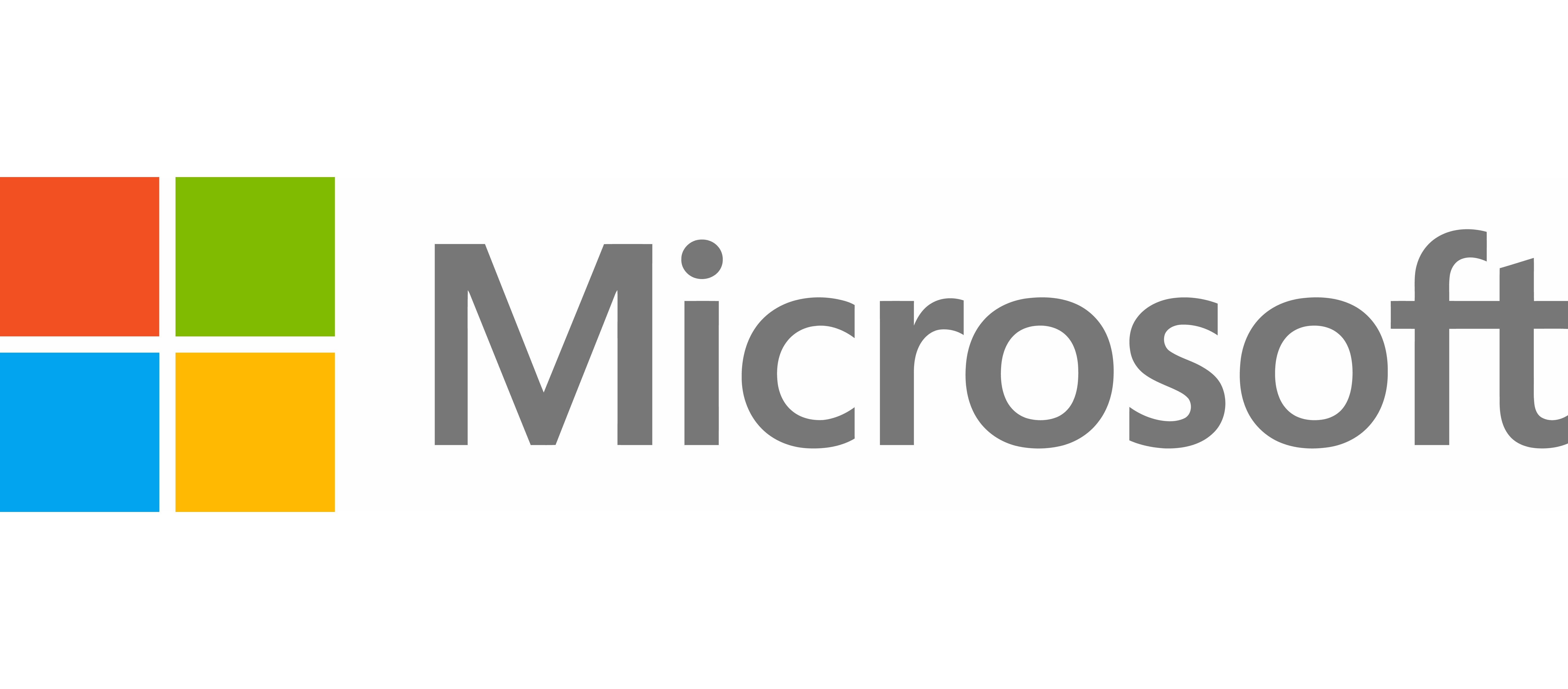
Microsoft
DAC Unit for Insitu PPHG Communication with Battery Cycle Tester
This student team will work to develop and design a DAC system that will take the digital output of the in-situ PPHG device and convert to analog voltage that is synced to Maccor Battery Test System. Design should be scaled to handle 48 in-situ PPHG units. Background: All batteries expand and contract as they are charged and discharged. Over time the battery thickness grows due to internal gases not recombining and growth of the SEI layer. This swelling can be accommodated in most devices (laptops, phones, etc.) by leaving an adequate gap above or below the battery. With a desire to keep devices thin this gap should be optimized. So, it is critical that we understand the battery swelling characteristics. Currently as the battery is cycled (charged and discharged) it is periodically paused so that someone can disconnect the cell or pack, remove it from the thermal chamber and manually measure the thickness. This data then is manually added to the Battery Cycler Data to track swell with cycle number. This is a very labor intensive process. Microsoft Battery Development Team has developed designed and patented an insitu PPHG (Parallel Plate Height Gauge) that resides in the chamber. This insitu PPHG can continually monitor the battery thickness and enables greater characterization of the battery with the capability of tracking the battery breathing. Battery breathing allows the Battery Engineers to understand the effects of different charge and discharge rates on the expansion and contraction as well as detecting peak swell where the manual method did not. This also saves large amounts of labor costs by eliminating the need for someone to interrupt the testing process to physically measure the thickness. This not only provides additional scientific value but also financial value as well. Problem & Requirements The output of the gauge is a digital signal. The Maccor Battery Test system can only intake analog signals. So a DAC is needed to convert the gauge signal to a form the Maccor can use. It is critical that this data be properly synced to the Maccor cycle data so the breathing can be aligned to where the battery cycle is at. • A rudimentary DAC was kluged together to validate the gauge design. This used an Arduino DUE1 as the DAC and connected to the Maccor system. This design does not scale. A scalable design is needed to propagate this new characterization system to the entire battery lab. • Given the digital output of the gauge and daisy chain design for the interconnect using a common serial bus interface (SMBUS, CAN, I2C). This minimizes the cable count leaving the Thermal Chamber. • It is preferred to have a system comprise of 48 PPHG encoder channels (Maccor channels counts are 48 or 96) • The Interface unit should be easily serviceable and repairable • The interface unit should fit into standard Rack form factor (2U max preferred).
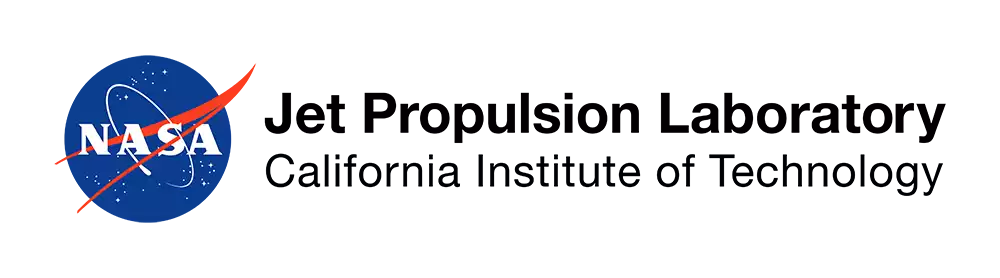
NASA Jet Propulsion Laboratory
Data Analysis for Multi-Hazard Risk Science: Risk and Resilience of Societal Critical Infrastructure to Space Weather and Compounding Natural Hazards
This student team will work to explore the characteristics of space weather impacts on critical infrastructure, specifically the power grid and communications systems. This student team will work to utilize a machine learning model to predict outcomes in various cases and identify non-obvious connections. This student team will work to build on the work of last year's student capstone team project. This student team will work to integrate data from the solar wind, geospace environment, and the critical infrastructure to study the systems effects. This student team will work to apply extreme value analysis (estimate of 1/100 year conditions), network analyses (understand the connectivity of the critical infrastructure), and machine learning (predictive capabilities). The student team will work to accomplish the following programmatic milestones and processes: - Create analysis ready datasets - Development plan/approach -Space Weather Extreme Value Analysis 1/100 year estimates and quantile-quantile results -Interconnect space weather hazard to other hazards (e.g., terrestrial weather) and identify candidate multi-hazard events -Multi-hazard initial results (via network analyses and machine learning) -A report out and conference/workshop presentations The student team will work toward the following outcomes: -Updated extreme estimates for space weather on the power grid and in regional manner (1 in 100 storms) -A machine learning model that can predict geomagnetically induced currents (GIC)’s spatiotemporally performs well on withheld (test) data. -Quantitative metrics of performance of multiple machine learning models. -Specifically graph network models. -Incorporation of extreme estimates for wind, temperature, and precipitation -List of candidate multi-hazard events that have cause power grid disruption for deeper exploration
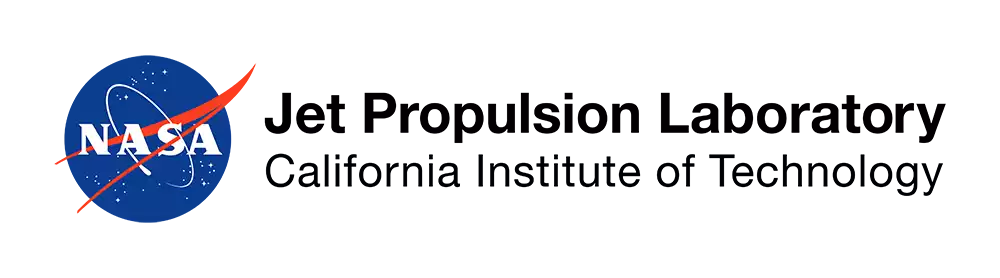
NASA Jet Propulsion Laboratory
Determining Lunar Regolith Properties Through Distributed Sensor Packages
The goal for the student team is to determine the properties of lunar regolith through distributed sensor packages on the moon. This will provide ground truth for remote sensing observations. As a first step, the student team will build a rough version of AstroJacks from JPL provided hardware, programmed, use network to find each other's locations, and determine Earth soil properties based on accelerometer data. This will develop skills on assembling hardware, writing software to operate it, and then taking test data using this hardware and software, which provides valuable experience in creating an electrical/software system. JPL will provide the student team with Raspberry Pis and Arduinos, and a variety of sensor, power, and communications hardware. These will be assembled on a breadboard and programmed using F'prime, JPL's open-source flight software. After building this hardware, the team will then have the sensors be able to determine each other's relative locations with signal strength, and determine the difference between being dropped on soft soil (sand) and hard soil (packed dirt). The goal is to determine each sensor's location to within 1 meter, across 30 meters of distance, and the difference between sand and packed dirt. It is a bonus if students can use machine learning to better predict soil types based on landing, and a greater variety of soil types. The student team will work to deliver to JPL the F'prime software capable of running on the sample platforms. The key desired outcomes are that these platforms can locate each other and provide input on the properties of the soil they land on.
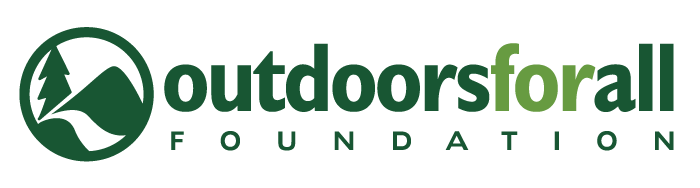
Outdoors For All Foundation
Bicycle Arm Prosthetic for Fittings
Outdoors for All is looking for a light-duty arm prosthetic for people with amputations or limb-differences to try riding a standard bicycle or recumbent trike with two points of contact at the handlebar. While a bike's controls can be moved to one side of the handlebar and people can balance and ride with one arm, it is safer to have two points of contact at the handlebar for steering, balance, and body-weight support. This device would allow students to practice planning, designing, and producing a mechanical product that would impact an underserved population. The product this student team is working to develop should easily attach to the handlebar of a standard bike and be adjustable for many different users. This is not intended to be used in aggressive or technical riding such as mountain biking, but rather as a fitting and trial tool to inform the user of whether purchasing a more expensive dedicated prosthetic is a good decision for them. The prosthetic the student team will work to design should be adjustable for different lengths, children and adults, left or right side, with both above and below the elbow capability. It should have a universal socket to accept the users residual arm and a way to attach securely to the elbow or shoulder. It can articulate to simulate elbow and wrist movement. It should be able to bear the users upper body weight, but does not need to support aggressive biking - just test riding. The outcome this student team will work to achieve is a product that Outdoors for All can use at its Adaptative Cycling Center or other programs to conduct fittings and trials of bikes.
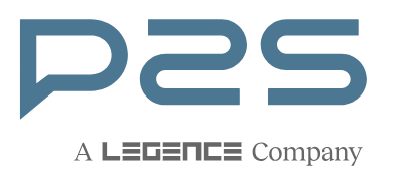
P2S
UW Shell House Renovation - Net Zero Concept Design
The student team will work with P2S mechanical engineers to develop a conceptual design to achieve net zero energy usage at the historic Shell House on the University of Washington Seattle campus. Students will gain an understanding of load calculations, mechanical system selections, energy modeling, methods to reduce and recapture energy, and methods to reduce carbon footprint. This student team will work to use the fundamentals of Heat Transfer, Thermodynamics, and Fluid Dynamics to determine how best to select, design, and evaluate energy performance of mechanical systems. Project design elements this student team will work to incorporate include calculations, energy modeling, system selection, layout of the design in CAD/BIM software (as available), and report writing. The desired outcome this student team will work to achieve includes an understanding of facility mechanical design, energy modeling, and impacts to our environment. Deliverables include calculations, drawings, and reports.

PACCAR
E-Truck EV Charging Subsystem Development
The student team will work to: - Evaluate different charging systems and charging protocols and finalize the charging systems that will fulfill the project’s requirements. - Investigate and finalize the routing, mounting and location of the charge inlet port. - Simulate the charging cycles to help with developing the charging controls. - Develop charging controls (includes but not limited to basic functionality, safety functions and derate strategies) - Develop test bench and a software simulation to verify the software. - Submit the final software, test procedures, wiring diagrams, and subsystem integration details of the energy generation subsystem as a final project deliverable. The student team will work on: -Component selection -Component location, mounting, routing -Component integration on the vehicle -Software development -Software verification The student team will work towards the following outcomes: -Develop charging controls (includes but not limited to basic functionality, safety functions and derate strategies). -Develop test bench and/or a software simulation to verify the software. -Submit the final software, test procedures, wiring diagrams, and subsystem integration details of the energy generation subsystem as a final project deliverable.

PACCAR
E-Truck HMI Design and Development
This student team will work to design a human-machine interface (HMI) for the UW E-Truck RSO. E-Truck currently has four technical teams—Structures, Systems, Control, and Electrical—that will concentrate on engineering development for the 2024-2025 year. This project will follow a human-centered design (HCD) model (Empathize, Define, Ideate, Prototype, Test) in alignment with PACCAR's industry design standards to create a development-ready dashboard interface. Throughout each phase, students will work to collaborate closely with sub-team leads to ensure that the HMI system is feasible given the truck's current electrical capabilities. In addition to the physical development of the HMI system, students will work cross-functionally with E-Truck engineers, PACCAR UX designers, and Electrical/CS engineers. Key design parameters for this project will ensure that the HMI is functional, safe, and user-friendly, addressing both the needs of the driver and the technical constraints of the vehicle's systems. The interface should have a simple and intuitive design that allows users to access critical information (e.g., speed, battery status, navigation) with minimal effort and key informational hierarchy. Performance will be tested and validated by real truck drivers for qualitative feedback of the HMI experience. In addition, designs will also be tested using the system usability score (SUS) to benchmark its performance against other EV car and truck HMI systems. The desired outcome this student team will work to achieve is a development-ready HMI prototype for E-Truck, with benchmark deliverables throughout HCD phases. Students will work to conduct user research to develop design personas, perform market research, and gather insights through surveys. They will focus on feature prioritization, feasibility analysis, setting design requirements, and culminating a validation test plan. Prototyping will involve storyboarding, wireframing, and creating a minimum viable product. Finally, students will work to collaborate with E-Truck technical teams to integrate the system into the truck’s dashboard and carry out real-world user testing to refine the HMI. The desired outcome this student team will work to achieve is a development-ready HMI prototype for UW E-Truck. The stretch goal for this capstone is mounting the HMI.

PACCAR
E-Truck Powertrain and Braking
The E-Truck project is a 4-year project to convert a diesel medium-duty truck to a battery electric vehicle. This student team will support this effort by focusing on the powertrain and braking sub-system design and integration. This includes working both with simulations and physical components to define and execute the intended functionality to move and stop the retrofitted truck. This student team will build on defined requirements from prior efforts and collaborate with other capstone teams (as partners) and the E-Truck Registered Student Organization (RSO) (as a customer) to specify the interfaces (e.g. between the eAxle and the battery), create software to communicate with other systems via CAN protocols, and evaluate overall system performance to meet defined mission. This student team will work within the following design parameters and performance: -All research and design work will build on prior studies and structural analysis to avoid re-work. -The resulting powertrain sub-system must perform under operational conditions (P&D drive cycle, environmental, etc.) as specified by RSO. -Software developed must undergo Hardware-in-the-Loop verification to ensure compliance with road-worthy product rules. This student team will work toward the following outcomes: 1. Finalize drawings, CAD, and structural analysis for all major components installed (e-axle, driveshaft, etc.) 2. Define system requirements and architecture, both elements and interfaces internal to powertrain and at the system boundary. 3. Evaluate system performance for selected components (e-axle, batteries, brakes) via simulation and HIL (requires SW code for later integration with physical components). 4. Create simulation and bench prototype for regenerative braking system (requires accompanying code and physical components).

PACCAR
E-Truck Storage and Distribution System
This student team will work to: -Evaluate different HV and LV architectures (includes HV Battery, Power Distribution Box, LV Battery, Step Up/ Down converters etc.) and finalize the energy distribution subsystems that will fulfill the project's requirements. - Investigate and finalize the routing, mounting and location of the HV and LV architecture components. - Develop integrated controls for HV and LV architecture (includes but not limited to basic functionality, safety functions and derate strategies) - Develop test bench and/or a software simulation to verify the software. - Submit the final software, test procedures, wiring diagrams, and subsystem integration details of the energy distribution subsystem as a final project deliverable. The student team will work on: -Component selection - Component location, mounting, routing - Component integration on the vehicle - Software development - Software verification The desired outcomes for this student team include: - Develop integrated controls for HV and LV architecture (includes but not limited to basic functionality, safety functions and derate strategies) - Develop test bench and/or a software simulation to verify the software. - Submit the final software, test procedures, wiring diagrams, and subsystem integration details of the energy distribution subsystem as a final project deliverable.

PACCAR
E-Truck Thermal Systems
The E-Truck project is a 4-year program to convert a diesel medium-duty truck to a battery electric vehicle. This capstone team will support this effort by focusing on the thermal management systems of the vehicle. This involves engaging with both simulation and the physical hardware components needed to manage the vehicle's thermal systems for heating and cooling. The student team will leverage the established cooling, heating, and design requirements from previous efforts and collaborate with other capstone teams, as partners, along with the E-Truck Registered Student Organization (RSO), as the customer, to define the interfaces. Thermal management hardware will be integrated to the chassis to optimize space, routing, and weight. The team will create vehicle control software to manage the different thermal systems and implement safety features to safeguard critical components. This will require communication with thermal system sensors, actuators, pumps, and other vehicle systems utilizing J1939 CAN Protocol. The team will evaluate the thermal management performance with simulation and as an integrated system to ensure the project's objectives are met. Design parameters include: 1) All research and design work will build on prior studies and structural analysis to avoid re-work. 2) The resulting thermal sub-system must perform under all operational conditions (P&D drive cycle, during battery charging, defined environmental, etc.) and contain critical safety functions as specified by the RSO. 3) Software developed must undergo Hardware-in-Loop verification and a Vehicle Pass-off test on a closed course (or at the PACCAR Technical Center) to ensure compliance with road-worthy product rules. The student team will work toward the following outcomes: 1) Complete the drawings, CAD models, and structural analysis of the thermal management hardware installed on the vehicle, including components such as the radiator, HVAC system, cooling lines, and fans. 2) Define system requirements and architecture, both elements and interfaces internal to the thermal systems and the system boundary. 3) Develop control logic for the thermal systems that integrates all sensors, pumps, and actuators to ensure that heating and cooling meet all specified RSO requirements. 4) Create a thermal systems control logic that ensures safety features are functional on critical components. 5) Evaluate the thermal system software functionality (control and safety) and CAN interfaces via Hardware-in-Loop. 6) Create simulations (and possible bench prototypes) to analyze the thermal system performance under worst-case operating conditions for the respective thermal systems.

PACCAR
E-Truck Vehicle Controls
The electrification of trucks presents a range of intriguing vehicle control challenges. For example, integrating an electric drivetrain necessitates the development of a control architecture that seamlessly connects the electrical system with the truck's other components. In this project, the student team will build upon the control architecture design initiated in last year's capstone, utilizing industry-standard tools. The team will explore low-voltage control architectures (such as Control Area Networks and PWM) and develop the corresponding control algorithms. The primary objective is to create an embedded test bench to evaluate the control algorithm for specific subsystems. Control Architecture should be modeled to provide a software/hardware-in-the-loop optimization capability. Completion of a test bench for verifying control algorithm and documentation is required. The student team will work toward the following outcomes: 1) Refined schematic of the control architecture of the original truck. 2) Develop simulink-based software for the vehicle-level ECU. 3) A test bench which supports CAN communication with the team-selected controller (s). 4) Supporting documentation: a manual for test bench, design assumptions, design requirements/specifications, test data and result analysis, safety, and discussion and limitations of the chosen design.
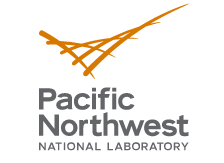
Pacific Northwest National Laboratory (PNNL)
Internet of Things of the Sea
Ocean observing systems have always been data limited for many reasons: harsh environment, expensive infrastructure, and low bandwidth communication options to name a few. This student team will work to create a low-power, open source, high speed underwater communication network to bring connectivity to sensors for real-time data acquisition. This project will require electronic design and software protocol development for a wireless connection between a seafloor platform (10-30 meters water depth) and closely located surface buoy. The communication network the student team will work to create can be based off existing protocols but adapted to work in a noisy underwater landscape. Performance goals for the student team: Data rate of 10Mbit/s, power less than 1 watt, intelligent and reliable software design which adjusts to environmental conditions: sea state, water clarity, sediment interference, etc. The subsurface unit will need to be enclosed in a watertight pressure housing, powered by batteries and capable of interfacing with external sensors for data transmission. The surface buoy needs to be solar powered and have a cellular or Wi-Fi connection to land. The end product will be deployed at PNNL Sequim Bay test site. The student team will work to create a functional prototype of a wireless communication system for underwater use. This should include the physical electronics, schematics, and bill of materials and whatever enclosures or containers used to house the setup. A GitHub repository of the software developed for the wireless communication.
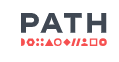
PATH
Using Machine Learning to Predict Climate Risk to Healthcare Facilities and Water Sources
As the climate changes globally, some regions will be more at risk of climate-related events such as floods, droughts, and extreme storms. This has a direct impact on the availability of clean water and there is an extreme and growing need to predict these risks in advance. PATH and a UW HCDE student team will work to identify areas and facilities which should be prioritized for climate-resilient improvements in order to maintain their access to safe water. Doing so will involve considering HCDE factors such as communication of scientific data and web interface design. Students will also use engineering skills related to machine learning and data analysis. A large amount of data exists surrounding climate and weather predictions. Similarly, data exists that details what water sources are available in different parts of the world, as well as knowledge about how these water sources respond to climate change. A hospital that relies on rainwater, for example, is at high risk of losing access to water if climate change affects rainfall. Students will use machine learning methods to a) identify health care facilities whose water supplies are susceptible to climate change and b) prioritize which facilities should get improved water sources first. Data and requirements will be sourced from public databases and stakeholder interviews. This student team will work to compile final results in a website or similar user dashboard by the end of the capstone term. This student team will work to develop and implement machine learning models that process data from multiple sources. Along the way, students will also write documents including a landscape analysis of relevant data types and other organizations working in this field who could provide expertise. Students will also compile their final results into a user-friendly and informative website.
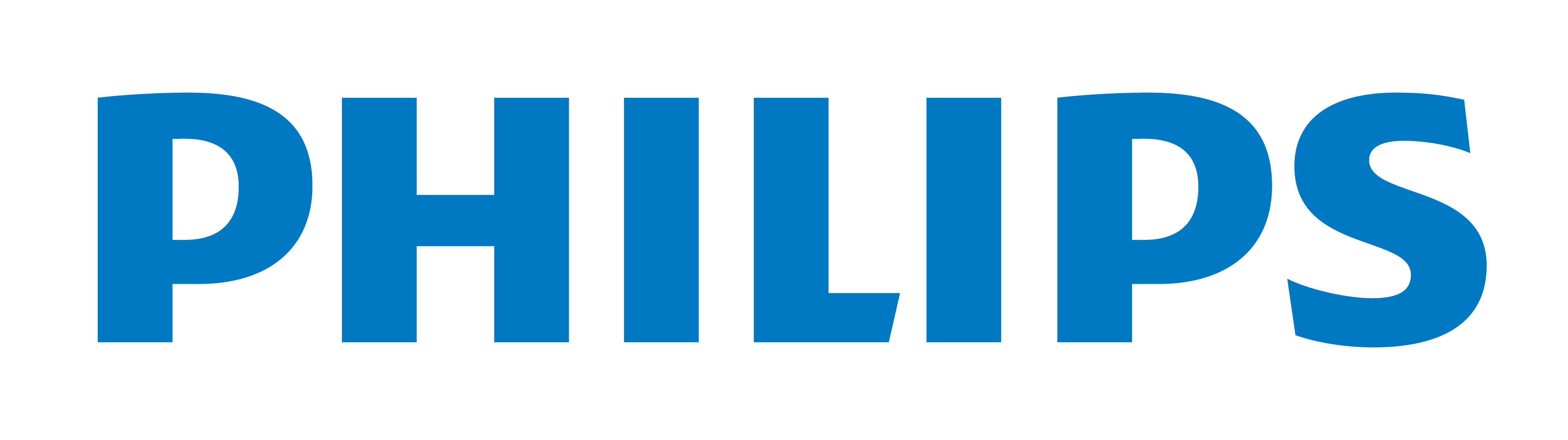
Philips
Power Toothbrush Head Defect Detection
Philips Oral Healthcare's supplier of toothbrush heads produces defects at a rate that exceeds Philips quality targets. The current process of defect detection includes a camera system and a manual human inspection, which has proven to be unreliable resulting in poor quality for the customer or excessive waste. Philips seeks to improve the inspection process to ensure the best quality brush heads for consumers and streamline their manufacturing to reduce time, money, and environmental impact. This student team will work to analyze defect data to find the best approach to reduce various defects in the brush head manufacturing line through device design or process improvements. This student team will work to design a solution to implement in the manufacturing process and accurately catch the specified defects during production. This student team will work to produce a prototype plan of the defect detection system to accurately catch defects. This student team will also have the opportunity to present the project onsite at Philips.
Related News
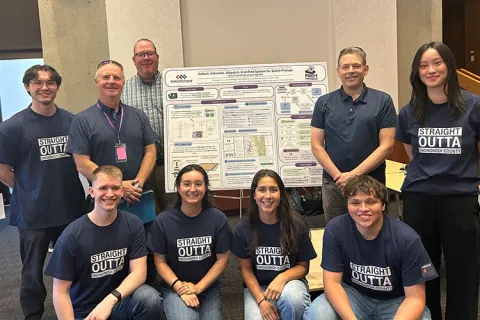
Thu, 07/17/2025
UW engineering students develop smart ballot solution
UW engineering students develop smart technology solution to improve ballot collection for Snohomish County.
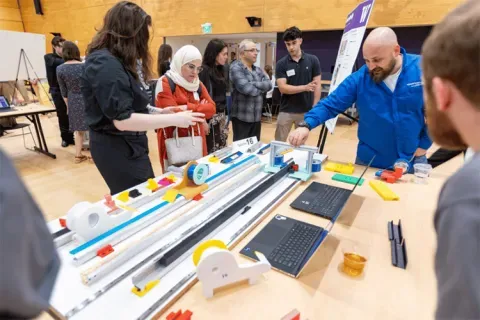
Mon, 07/07/2025 | UW Mechanical Engineering
Capstone creations
Students displayed innovative capstone design projects at the 2025 expo.
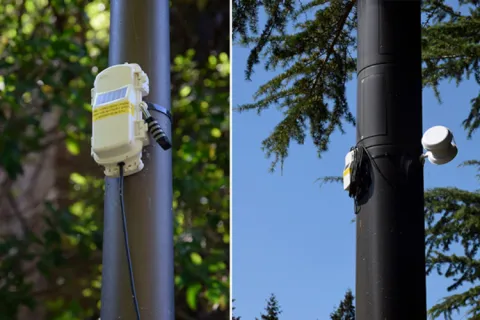
Fri, 09/20/2024 | UW Civil & Environmental Engineering
Smarter irrigation for a greener UW
A new project combines satellite data with ground sensors to conserve water and create a more sustainable campus environment.
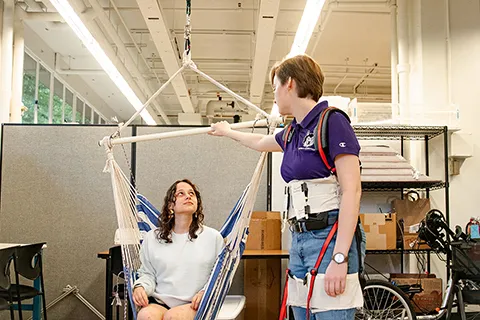
Mon, 09/09/2024 | UW Mechanical Engineering
Testing an in-home mobility system
Through innovative capstone projects, engineering students worked with community members on an adaptable mobility system.