Industry-Sponsored Student Capstone Projects
2021/2022
In the 2021/22 academic year the industry capstone program was supported by 62 sponsors and 95 real-world projects. Over four hundred students from across the College of Engineering participated. Scroll down to learn more about each project.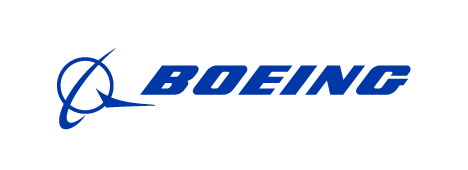
Boeing
BCA Quality Inspector Optimization
BCA Commercial Airplane Programs use different models to forecast quality assurance (QA) staffing and measure performance. One goal of Boeing is to drive stability throughout the production system with focus on quality as a key enabler to the overall success of the Boeing Production System. This student team will work to identify opportunities for improvement in both forecasting and allocation of Quality resources, daily work assignments, accountability metrics, and ensure alignment to the overall Boeing Production System. The team will work cross-functionally with QA, IE, Engineering, and Manufacturing Operations to conduct research and create recommendations.
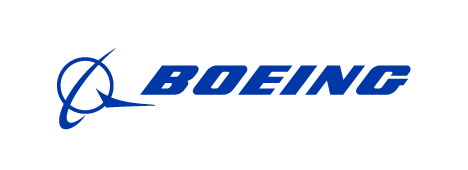
Boeing
Characterization and Application of Recycled Carbon Fiber
Aerospace and other industries have increasingly utilized carbon fiber composites as a structural material due to the design and manufacturing benefits the material offers high performance products. As the use of composites increases, the recycle-ability of the material has been addressed so that like metals, the scrap and other by-products can be recycled to be used in a circular manner in other products. The carbon fiber is the most valuable component to recover for second use. Carbon fiber recovery processes have achieved pilot and production scale operation by means of chemical and thermal recovery processes to support increasing needs for carbon fiber recycling. These processes all share the common downstream market capacity challenge of recovering discontinuous largely random filament material forms (non-woven broadgoods, milled and chopped short fiber) as compared to virgin fiber continuous form. Processing and properties for recycled fiber non-woven broadgood composites have been explored and openly published. There is a need for process development, performance characterization and benefit assessment for hybridized use of recycled carbon fiber materials with virgin fiber materials such as, but not limited to, unidirectional tapes and fabrics to improve consideration and adoption of these sustainable materials for environmental benefit. The scope of this project includes but is not limited to fabrication of control and hybrid mechanical test panels, mechanical testing of those panels, assessment of potential market applications, and life cycle analysis for environmental benefit. The student capstone team will work to develop a working knowledge of fiber reinforced composites with hands-on experience designing, processing and testing laminates. Deliverables should include (1) a literature search on current state of the art, (2) Test plans for processing and characterization of hybrid options to be determined by the team with laminate design and test iteration. (3) A test report with results from processing and mechanical characterization (4) Selection of potential application(s) that can leverage advantages of hybrid performance along with a life cycle analysis based on anticipated demand, use of rCF material as compared to existing materials and designs. (5) Optionally fabrication and test of a demonstration exploration article.
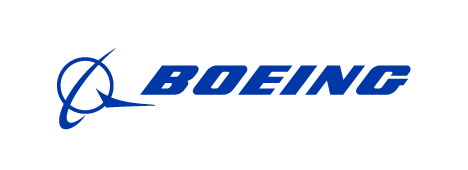
Boeing
Experimental Bolted Connection Calculator
Connection analysis is inconsistent across the UW FSAE team. This student team used analysis methods detailed in Air Force Stress Manual and tests they developed to create and validate a joint strength calculator to predict strength of common fastening systems used across the FSAE team. The team also produced a test report to validate the joint strengths derived by the calculator. The calculator can be used throughout the FSAE team to reduce the time/cost needed to design and analyze joints between interfacing teams.
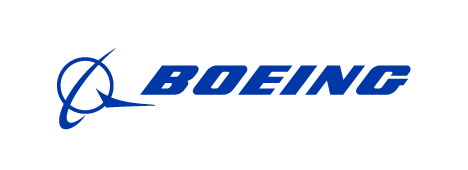
Boeing
Mechanical Fixture Development for Surface Treatment of Thermoplastics
Proper surface preparation is vital for proper bonding during manufacturing rework and field repairs. A plasma treatment can aid significantly but must be carefully controlled to ensure adequate speed, standoff, and coverage across a range of aircraft surface curvatures and orientations. A UW capstone project last year considered several design alternatives and selected a potentially viable solution using a belt gantry system. The lab-tested prototype resulted in several recommendations for improvements for future consideration, including the use of custom software for better UI, better wheel design, improved tolerance control and additional safety features. This student team worked to incorporate these recommendations and fabricate a mechanical fixture with an increased readiness level for practical use on airframe structures. They created a proof-of-concept demonstration of the fixture – one that demonstrates the fixture’s capabilities to raster a curved aircraft surface (or an equivalent composite panel) with a portable compact plasma nozzle system within the specified surface treatment parameters.
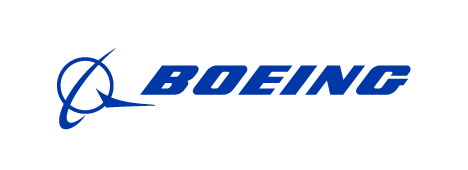
Boeing
Metal AM Finishing Fluid Flow Modeling
Additive Manufacturing (AM) is quickly transforming industrial manufacturing with the ability to produce high strength, low weight parts with intricate designs that are too complex to manufacture by conventional methods. However, the finishing/smoothing of parts remains one of the biggest challenges for enabling full and affordable implementation of AM. This student team worked to create a model that accounts for reaction kinetics, gas production, and gas and fluid flow and how it interacts with intricate part shape to design an optimal chemical processing configuration on internal surfaces, including the effects on the local metal removal rate on a complex geometry part. This was validated with chemical milling an aluminum or stainless steel part.
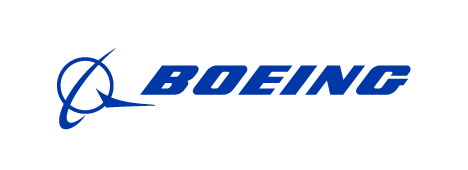
Boeing
Portable Plasma Process Window Definition for Thermoplastic Surface Treatment
Non-traditional surface treatment methodologies like atmospheric plasma, laser treatment, and UV light have been shown to activate inert bonding surfaces. Particularly in thermoplastic substrates, these methodologies present promising options for adequate and robust surface treatment prior to structural bonding. Structural repair of thermoplastics requires specific plasma treatment parameters to be controlled - speed, number of passes, overlap, and stand-off distance between the substrate and the plasma source. Bonding of thermoset repair material to damaged thermoplastic substrates is currently being evaluated as a more practical repair method as opposed to welding of thermoplastic repair material. Currently, a set of plasma treatment parameters are being used to achieve a robust structural repair of thermoplastics. The student team investigated and defined the process window for plasma surface preparation using the Plasmatreat RD2004 portable unit for repair applications.
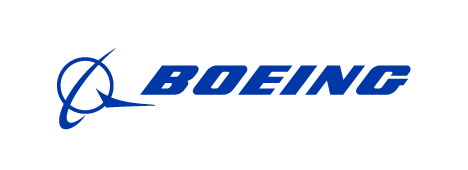
Boeing
Powder Bed Fusion Build Process Interruption Study
Additive manufacturing (3D printing) with metals has the potential for significant weight savings in aerospace applications, along with numerous other advantages. To realize these advantages, the sources and amounts of variability in component strength and fatigue properties must be well understood. A “round robin” study started at UW last year focused on intra-build, intra-machine, and inter-machine variation using a EOS M290 printer to laser-sinter titanium components. This capstone will expand this study to better understand additional sources of variation, such as typical process parameters and the effect of build interruption. Students will examine the existing data and design samples, experiments, and an interruption procedure to test important factors affecting variation. ME prerequisites: None
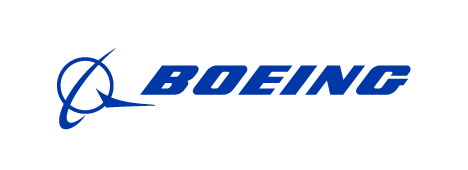
Boeing
Thermoplastic Additive Manufacturing Finishing Process
Additive Manufacturing (AM) is revolutionizing the way we fabricate aerospace components by enabling increasingly complex part designs. The Fused Filament Fabrication 3D printing process has many advantages including the ability to print one-off replacement parts. However, the resulting substrates are porous throughout the part, similar to a solid sponge, which makes them difficult to smooth and finish. The student team worked to study the print parameters for an optimized porosity at the part surface, completed a paper study on potential smoothing options, and provided recommendations on the best technique.
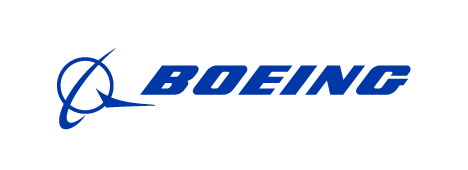
Boeing
Thermoplastic Ultrasonic Welding Process Development
The ultrasonic welding technique is an ultra-fast joining process, and it is used to join thermoplastic composite structures, and provides an excellent bonding strength. Boeing and a 2020-2021 UW capstone team started an investigation into characterization of weld process and joint strength of ultrasonic welding, but strong conclusions were not able to be drawn from the data. This student team worked to continue to characterize ultrasonic welding process and joint performance for thermoplastic composites, which have aerospace applications in interiors with PEI materials and primary structure with PEEK/PEKK. The team analyzed raw coupon testing data and weld quality data to characterize joint strength and recommended welding process parameters to optimize joint performance.
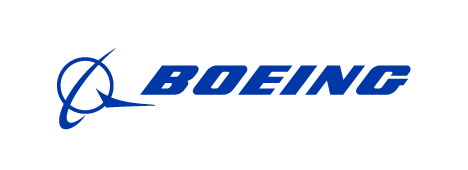
Boeing
Utility Freighter Aircraft
Air cargo remains a key element of global trade carrying 35% of total trade measured by dollar value. The value of air cargo to world trade has been further highlighted during the COVID-19 pandemic, as the need to ship critical medical supplies and equipment quickly, securely and over long distances has been underscored throughout 2020. There is a forecasted increasing demand for freighter aircraft in the next 20 years, based on a growing freight market and replacement of ageing aircraft. However, one potentially underserved area is easily moving freight to and from outlying areas to the larger cargo hub airports. These areas are traditionally served by small cargo aircraft or by road trucks, where cargo needs to be unpacked and repacked for the smaller transport. Particularly in a pandemic environment, this slows down distribution of critical supplies to outlying areas, as well as getting perishable goods from these outlying areas quickly and efficiently to market. The student team worked to create and validate an aircraft design that can carry main deck ULDs and/or pallets and that can be loaded and unloaded at smaller, remote airports, where ground handling loading equipment may be limited.
Booz Allen Hamilton/UW Applied Physics Laboratory (APL)
UW Human Powered Submarine (HPS) Autopilot Project - Test Phase 1
This student team built on the development of the prototype Autopilot module, developed a validation and verification test regimen, and conducted bench testing in a simulated environment with the goal of providing the UW Human Powered Submarine (HPS) team with a fully bench-tested working prototype of the Autopilot module for incorporation into the current HPS design. The objective of the validation and verification testing was to ensure the autopilot sensor can tolerate off-axis installation in the actual vehicle and can tune control surface outputs based on actual control surface deflection areas and lever arms off the vehicle center of rotation.
City of Fife
Fife City Hall and Vertical Evacuation Structure and Evacuation Planning
This student team worked on programming and preliminary design of a new City Hall and sitework, to include a vertical evacuation structure for potential lahar and tsunami events. The City of Fife lies in the Puyallup River valley and has, over geological time, been subject to both lahar and tsunami events. Seismologists state that such events could occur again, including some risk that a major earthquake in the Cascadia Subduction Zone could trigger both a tsunami and a lahar. In such a case, the tsunami might hit Fife ten to fifteen minutes after the earthquake and the lahar less than an hour after that. Despite this risk, the City's proximity to the Port of Tacoma and Interstate 5 has led to substantial development of the city, which now hosts over 20,000 employees and 10,360 residents. The team prepared conceptual plans and documents for a new building or buildings to house City Hall, police, and court functions, as well as to serve as a vertical evacuation structure that will protect occupants in the event of a lahar.
Coupang
Image Quality Control for Coupang Catalog
Coupang is an international e-commerce platform that hosts billions of sellable items. At the time of this project, human operators are performing quality control on only a small number of seller listings, a process that cannot be scaled as the business grows rapidly. The student team worked to create scalable models to improve image quality control for the Coupang marketplace including detection of unwanted elements and image super resolution.
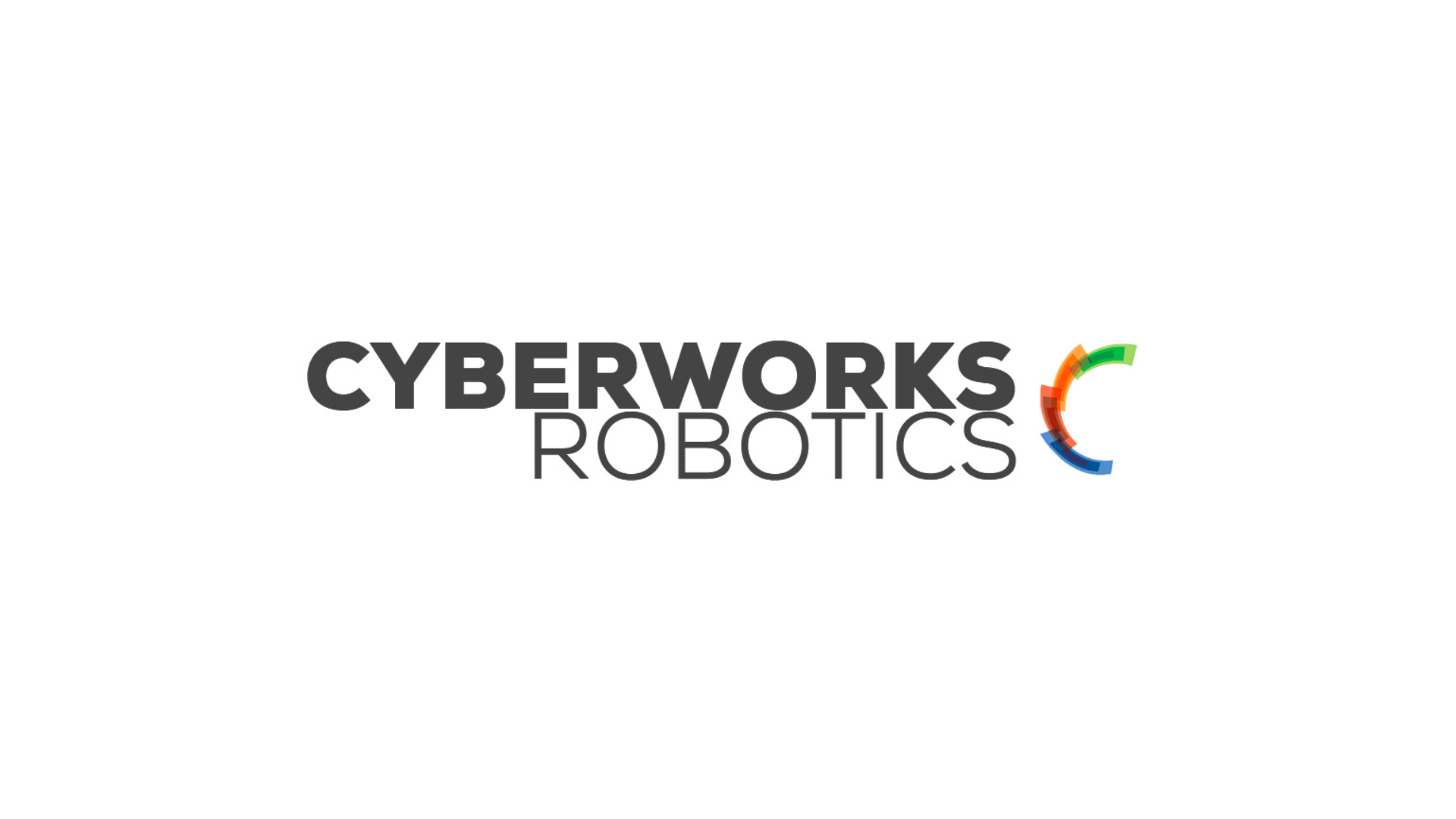
Cyberworks Robotics
Low-cost Perception System and Remote Management of an Autonomous Wheelchair
Autonomous Wheelchairs increase freedom and ease of mobility for the most vulnerable peoples in society. This student team integrated sensors and developed a perception system for autonomous, campus-wide navigation, with the goal of reducing reliance on LiDAR based SLAM. The team also focused on integrating system fault detection and a remote wheelchair management system into the Cyberworks Autonomous Navigation stack.
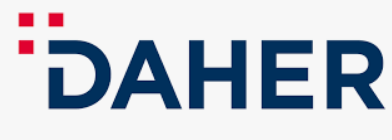
Daher
Assess the Effect of Crystallinity Degree on Mechanical Properties of a Thermoplastic Composite Structure
Daher is an aircraft manufacturer and an industry and service equipment supplier. The student team worked to assess the effect of crystallinity degree on mechanical properties of a thermoplastic composite structure. The team determined the degree of crystallinity with different time and temperature exposition, validated analysis through chemical and physical tests, built a time temperature transformation graph for different crystallinity, and identified cure cycle parameters to repair the crystallinity of a thermoplastic composite structure.
Related News
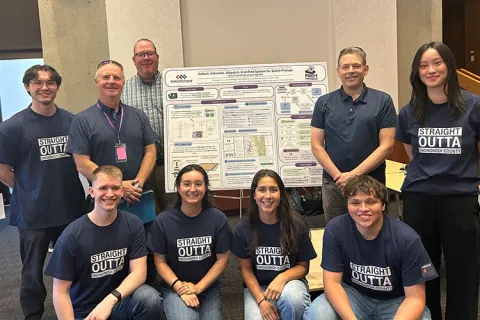
Thu, 07/17/2025
UW engineering students develop smart ballot solution
UW engineering students develop smart technology solution to improve ballot collection for Snohomish County.
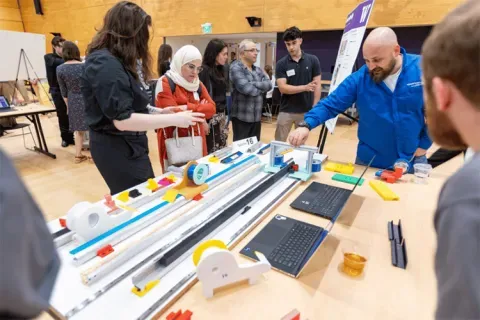
Mon, 07/07/2025 | UW Mechanical Engineering
Capstone creations
Students displayed innovative capstone design projects at the 2025 expo.
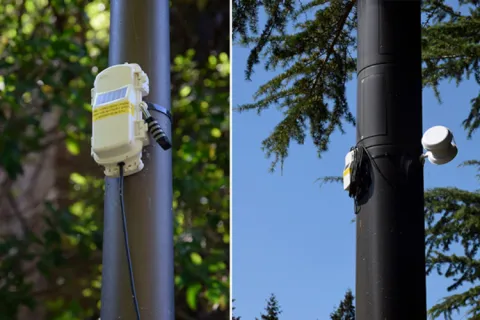
Fri, 09/20/2024 | UW Civil & Environmental Engineering
Smarter irrigation for a greener UW
A new project combines satellite data with ground sensors to conserve water and create a more sustainable campus environment.
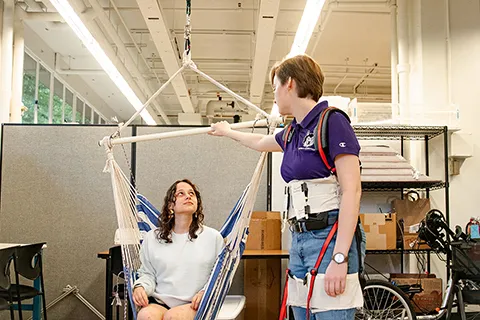
Mon, 09/09/2024 | UW Mechanical Engineering
Testing an in-home mobility system
Through innovative capstone projects, engineering students worked with community members on an adaptable mobility system.