Boeing
Flexible Positive Pressure Consolidation Expandables
Structural composite parts need to undergo high-pressure compaction and heating for curing, which is traditionally done using autoclaves. However, the cost of purchasing and operating an autoclave is significant. In cases where large composite parts that have already been cured in an autoclave require repairs in small areas, returning the large composite part to the autoclave is not cost-effective and causes further production delays, especially in industries like airplane manufacturing. A more effective repair method is needed: a solution that provides local compaction and heating without requiring airtight sealing and another large apparatus, such as an autoclave. This proposal seeks a solution where a localized positive pressure consolidation system that can achieve predetermined pressure of compaction (such as 15-50 psi) for a duration (such as one hour) at a predetermined temperature. This project is a continuation of a previous UW capstone project, which led to a proof-of-concept demonstration unit. This student team will focus on a more flexible system adaptive to curved parts that have the potential to be implemented in the aviation industry. The student team will perform two main technical tasks: 1) Develop a flexible setup that can be adaptive to various geometries. This setup should include features such as a flexible cover and a reaction support plate that can adapt to different shapes to counteract the positive pressure. 2) Monitor and control the pressure generated from the expandable material. The compact pressure should be high enough to create high-quality composite structures or high-quality bonds, but low enough to enable a reasonably reaction support plate to counteract the positive pressure. Additional requirements, such as surface finishes, may be needed depending on the applications. The tool will need to be cleaned after curing. The first two tasks can be based on a co-bond setup between metal and composite doubler. 3) Depending on the success of the first two tasks, a stretch goal is to make composite parts by using the system and compare the parts to two more fabrication methods: autoclave cured method and Double Vacuum Debulk (DVD) cured method. The student team will develop a flexible positive pressure consolidation system by using expandable media. 1. Generate ideas, evaluate them, and create prototypes. Key components include a flexible cover, pressure sensors, fastening elements, and a reaction support plate to withstand positive pressure. 2. Conduct initial validation tests at the component level for selected ideas based on the co-bond setup between metal and composite doubler.
Faculty Adviser(s)
Navid Zobeiry, Materials Science & Engineering
Related News
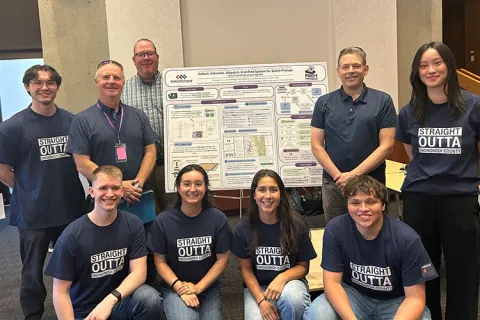
Thu, 07/17/2025
UW engineering students develop smart ballot solution
UW engineering students develop smart technology solution to improve ballot collection for Snohomish County.
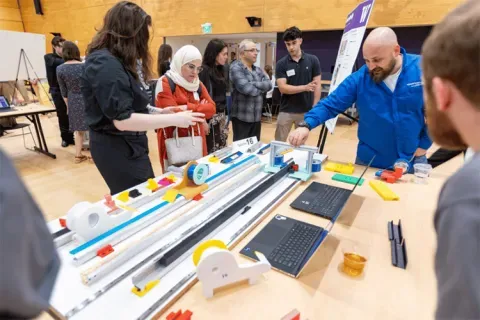
Mon, 07/07/2025 | UW Mechanical Engineering
Capstone creations
Students displayed innovative capstone design projects at the 2025 expo.
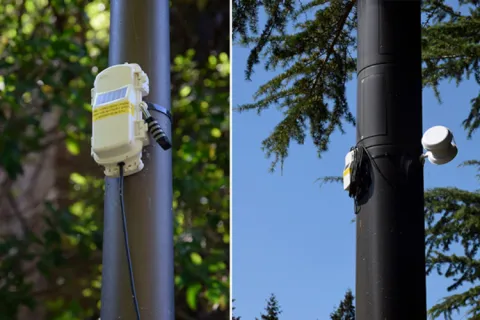
Fri, 09/20/2024 | UW Civil & Environmental Engineering
Smarter irrigation for a greener UW
A new project combines satellite data with ground sensors to conserve water and create a more sustainable campus environment.
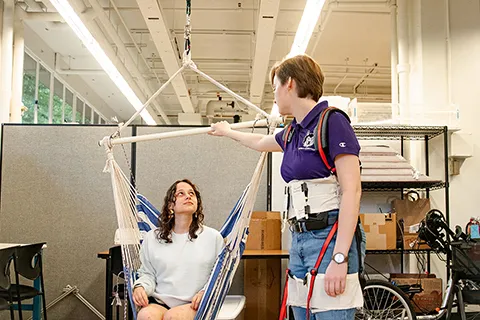
Mon, 09/09/2024 | UW Mechanical Engineering
Testing an in-home mobility system
Through innovative capstone projects, engineering students worked with community members on an adaptable mobility system.