UW Applied Physics Laboratory (APL)
Autonomous Underwater Instrument Retrieval
PROJECT DESCRIPTION AND SCOPE: From moored buoys and profiling samplers to autonomous robotic systems, in situ sampling is critical for the understanding of marine physical, biological and chemical processes. Developing technologies to emplace a sensor with the required data and power storage for the desired timespan, and to then successfully retrieve the data, is a core logistical challenge in ocean science. In many cases, the core sampling task can be performed by a simple battery-powered datalogger, but the infrastructure for emplacing the logger and ensuring it can be retrieved at project completion can be significant. This is particularly true for instruments placed on the seafloor, which require either retrieval by a diver or remotely operated vehicle (ROV), or a complex and bulky remotely-released recovery system. This creates a financial burden towards the kinds of projects that can be successfully deployed, reducing access to critical ocean science and monitoring. The goal of this project is to develop a prototype system for the autonomous recovery of emplaced instrumentation on the seafloor. It consists of a “smart hook”, based on the BlueRobotics BlueROV2 technology, which can carry a winch line from a waiting boat to the seafloor. Once there, it uses computer vision to identify and home to an object and attaches the winch line. The object can then be retrieved by the ship’s winch. Though conceptually simple, this approach greatly simplifies the process of subsea instrument recovery. It reduces the mass and complexity of the deployed instrument, requires no personnel in the water, and can operate beyond human diving depths. It does not rely on the ROV to carry the weight of the instrument, minimizing ROV size, and improves on adhoc solutions based on manual operation of non-specialized ROVs. DESIGN PARAMETERS AND PERFORMANCE: Students will design a subsea system for object retrieval. This includes the mechatronic adaptation of the vehicle and can also include design of a cooperative attachment point on the instrument which may include mechanical or visual features to assist with grasping. The vehicle will be designed to interface with a ships’ winch line and to guide the line to the recovered instrument, then attach itself. To the greatest extent possible, the target localization and attachment process will be fully automated. However, given the scope of the project, the prototype will focus on the use of computer vision for object localization. For this project, a nominal search area (based on GPS error circles) will be fixed. Students will design a computer-vision-based control system for guiding the ROV to the target and latching. The system will include a mechanism for verifying successful latch. We assume this system will remain tethered to the ship, using the existing BlueROV umbilical. However, the operational procedure must handle the logistical challenge of having both the vehicle tether and winch line in the water simultaneously, both during vehicle deployment and instrument recovery. System performance will be measured based on success in completing attachments as a function of water conditions (e.g. turbidity). System size, weight, power and cost (SWAP-C) will also be considered but given this is a first prototype, will not be the main determinant of system success. According to team needs, the system will be tested in the UW School of Oceanography Test tank or in fresh water near UW (ship canal, Lake Washington). OUTCOMES: Students will develop a full system prototype for automated attachment to cooperative objects on the seafloor. This will provide students with experience at the intersection of autonomy, robotics, and mechanical design. This will include a robotic system for attaching a ship’s winch line to the object and may also include an engineered attachment point on the object to promote successful grasping. Students will evaluate performance in a variety of water conditions and will detail areas of potential system improvement. Students will come away with knowledge in automation, underwater vision, manipulation, and interpersonal communication. Deliverables include: -A working prototype of the system. -All mechanical and electrical integration details will be documented and shared publicly under an appropriate open source hardware license through a project website / Github repos. -A report of the impacts of environmental damages to coastal communities. -Within the limits imposed by third-party tools used, all software will be documented and published in an open source manner through a project web site / Github repos. -Students will complete all required publications for CoE capstone program. -Ideally, students will participate in or produce additional media for program supporters.
Faculty Adviser(s)
Aaron Marburg, Principal Electrical/Computer Engineer
Related News
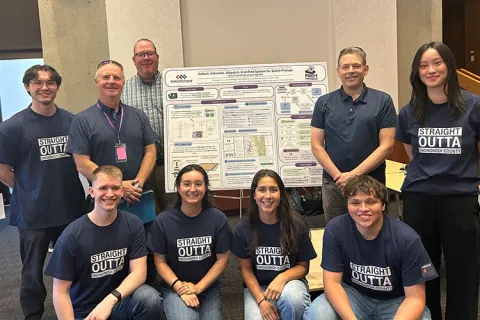
Thu, 07/17/2025
UW engineering students develop smart ballot solution
UW engineering students develop smart technology solution to improve ballot collection for Snohomish County.
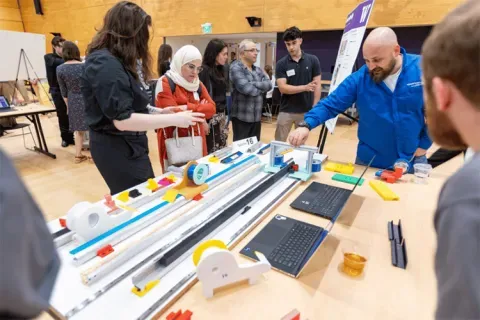
Mon, 07/07/2025 | UW Mechanical Engineering
Capstone creations
Students displayed innovative capstone design projects at the 2025 expo.
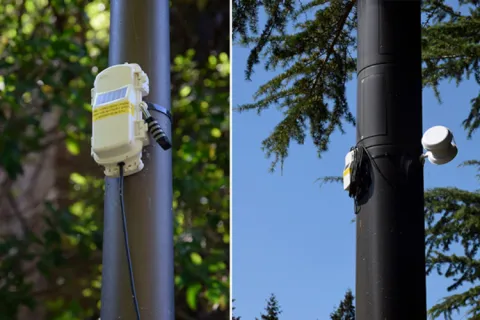
Fri, 09/20/2024 | UW Civil & Environmental Engineering
Smarter irrigation for a greener UW
A new project combines satellite data with ground sensors to conserve water and create a more sustainable campus environment.
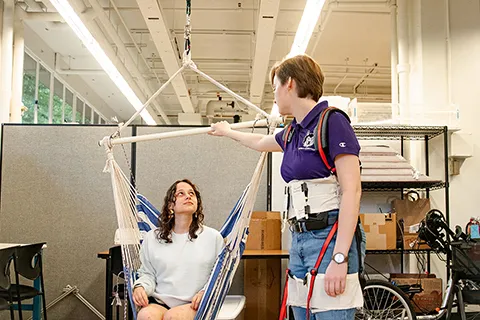
Mon, 09/09/2024 | UW Mechanical Engineering
Testing an in-home mobility system
Through innovative capstone projects, engineering students worked with community members on an adaptable mobility system.